Pallet Rack 101
When designing Pallet Rack Storage Systems you want to maximize the total usage of cubic square footage your building has to offer. The higher utilization of cubic square footage will effectively lower your total square footage cost.
Start by identifying what is going to be stored (i.e. Pallets, Skids, Totes, Boxes etc.) along with weight and dimensional requirements.
Understand what combinations of pallets represent the highest and lowest pick volumes. Identifying this will help determine the effectiveness of Material Flow in and out of the warehouse.
Design the rack system and then determine forklift equipment. Having narrower aisles will allow for more pallet spaces and greater utilization of Cubic Square Footage. The right equipment to operate in these narrow aisles is critical to maximize operator efficiency.
Think about how many pallet spaces you require now and what your expected growth is over the next 5 Years.
Work with a Material Handling Specialist to create an AutoCAD rack layout design.
Storage Mediums
Single Selective:
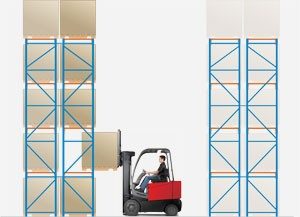
This is the most common design found in warehouses. It offers easy access to pallets as each pallet faces out into the aisle, which means that specialized forklifts aren’t required to select the stock. It’s well suited for companies looking to store a wide variety of products that need to be accessed quickly.
With its wider aisles, it’s well suited for mixed pedestrian & forklift movement, such as pallet in/case out. This allows you to store opened pallets on the bottom level, giving your staff easy access to individual packages of your products. The remainder of the stock can be stored in the levels above.
If you’ve been bulk stacking your pallets on top of each other, selective racking will allow you to safely store your pallets to a much greater height, maximizing the vertical space in your warehouse.
Double Deep Pallet Rack:
Well suited to storing a small to moderate variety of products which don’t require the same level of quick access as selective racking provides. Double deep racking allows you to store a greater number of pallets in the same space.
Double deep rack uses a deep reach truck (forklift) that can retrieve pallets several levels deep. If you have an existing selective rack system in place, double deep can be retrofitted to your existing system. This allows you to increase your pallet density without sacrificing your existing investment.
Drive-In Pallet Rack
As the name implies, Drive-In rack is designed to allow forklifts to drive into the lane to pickup or place pallets. This allows drive-in rack to store approximately 40% more pallets than a selective rack system. Drive-In rack’s flexibility allows you to use either counterbalanced or reach lift trucks to access your stock.
Very Narrow Aisle
Very Narrow Aisle rack works well when you have a large number of products that need to be moved in and out quickly. Pallets are always 100% available, and VNA’s height allows you to maximize the vertical storage space in your warehouse. A specialized VNA lift truck is required to pick pallets.
Aisles are reduced by 34% or more versus single selective rack, allowing you to increase your pallet density. Rack and product damage are also reduced as the truck travels straight through the aisle and picks pallets from either side.
Push Back Pallet Rack
With push back rack pallets are placed onto a cart, which is then rolled up a track by newly arrived pallets. Our push back racks can store pallets 2 to 6 deep and can be placed back to back, allowing you to store 12 pallets per aisle.
The footprint of a push back rack is similar to a drive-in rack, but the utilization tends to be higher resulting in better space savings.
Pallet Flow Rack
With pallet flow rack, received stock is placed on one end of the aisle and picked at the opposite end. This allows you to separate the picking and placing of your stock, preventing forklifts from fighting for the same space.
Pallet flow rack works best with a high level of activity and a small number of SKUs. Its flexibility allows counterbalanced or reach lift trucks to used with the system
Cantilever Rack
Cantilever rack is the most efficient way to store long bulky products. It’s typically used to store items such as building materials, piping, rolls, furniture, and sheet goods. The arms can be adjusted to suit the height of your products, and it can be configured for single or double-sided use.
Counter-balanced or reach lift trucks can be used with cantilever racking, and with 4-directional lift trucks narrow aisles are also a possible configuration.
Recent Comments